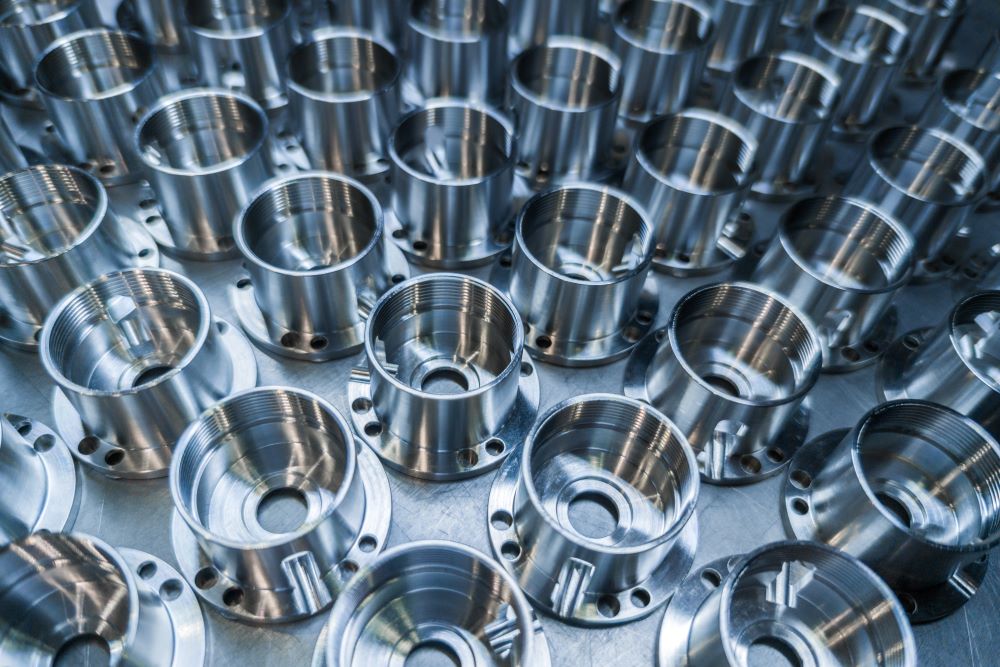
The metalworking fluid industry plays a crucial role in the manufacturing and processing aluminum parts. Aluminum, known for its lightweight and corrosion-resistant properties, is widely used across various sectors, including automotive, aerospace, and consumer electronics. However, maintaining the aesthetic and functional integrity of aluminum surfaces during manufacturing processes poses challenges, notably staining. Staining can occur due to improper handling, chemical exposure, or inadequate use of metalworking fluids. This article outlines effective strategies and products to prevent staining on aluminum surfaces, catering to engineers and machine operators in the metalworking industry.
Understanding Aluminum Staining
Staining on aluminum surfaces can manifest as spots, blotches, or discolorations, detracting from the material's appearance and potentially compromising its corrosion resistance. These stains are often the result of:
- Chemical Reactions: Interaction with aggressive chemicals or unsuitable metalworking fluids.
- Water Stains: Residue from hard water or improper drying.
- Galvanic Corrosion: Contact with dissimilar metals in the presence of an electrolyte.
- Machining Residues: Accumulation of oils, greases, and metal particles.
Best Practices to Prevent Staining
Preventing staining on aluminum surfaces requires a holistic approach, from selecting the right metalworking fluids to implementing stringent handling protocols. The following best practices are recommended:
- Proper Selection of Metalworking Fluids: Choose fluids specifically formulated for aluminum or multi-metals applications to avoid chemical reactions that can cause staining.
- Regular Maintenance of Fluids: Maintain metalworking fluids at the correct concentration and pH levels. Regular monitoring and filtration can remove contaminants that might lead to staining.
- Avoid When Possible: Avoid prolonged contact time with very sensitive alloys such as 7075, which can stain extremely quickly, even with water. Avoid pooling fluids and if possible, blow excessive fluid from the part.
- Control of Machining Conditions: Optimize machining parameters to minimize the generation of excessive heat, metal chips, and fines, which can contribute to staining.
- Thorough Cleaning and Drying: After machining, parts should be cleaned to remove any residues and dried immediately to prevent water stains. Very sensitive parts should be handled using gloves to avoid fingerprints and oil mark stains from human hands.
- Avoiding Contact with Dissimilar Metals: Prevent galvanic corrosion by ensuring aluminum parts do not come into contact with dissimilar metals, especially in the presence of an electrolyte.
Recommended Products
Several products have been developed to prevent staining on aluminum surfaces during the metalworking process. These include:
- Non-Staining Metalworking Fluids: Fluids specifically formulated for aluminum and non-ferrous metals, offering excellent lubricity without the risk of staining.
Chem Arrow offers several fully synthetic and semi-synthetic products that provide outstanding non-staining characteristics.
- ArrowCool SYN-726-B: A neutral-based, high lubricity, low foam product. It provides outstanding biostability and protects all grades of Aluminum (even sensitive grades) from staining.
- ArrowCool SEM-927: A multi-metal compatible product offering customers outstanding performance while protecting your Aluminum from discoloration.
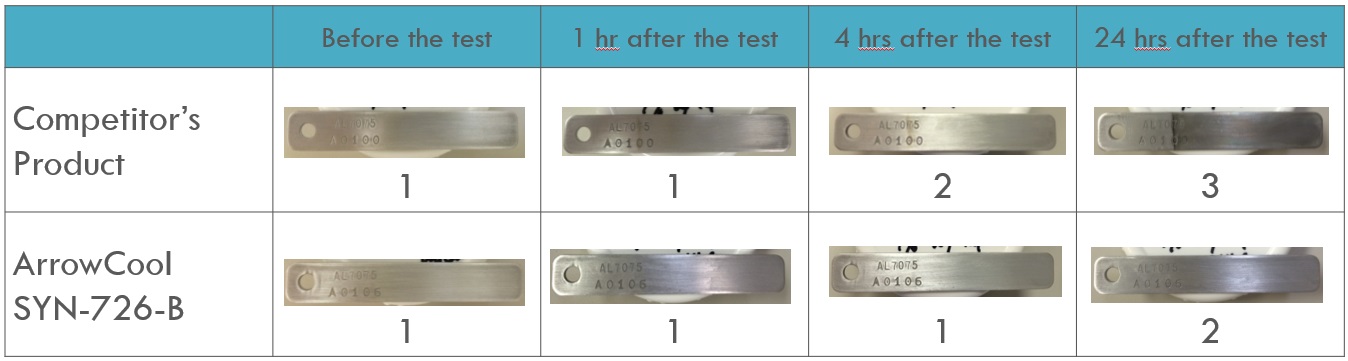
If you’re having staining issues with your current fluid, please contact Chem Arrow, or one of our distributors, to evaluate your current situation and provide you with some technical support to resolve this issue.
Conclusion
Staining on aluminum surfaces can undermine the aesthetic appeal and functional quality of aluminum parts. By adhering to best practices in the selection and maintenance of metalworking fluids, implementing appropriate cleaning and handling procedures, and utilizing specialized products designed to protect aluminum, engineers and machine operators can significantly reduce the risk of staining. These measures not only preserve the integrity of aluminum components but also enhance their longevity and performance in their respective applications. The collective effort in selecting the right processes and products is essential in maintaining the high standards expected in the aluminum manufacturing industry.